AlSiC作為封裝材料的基本特點有哪些?
一、AlSiC作為封裝材料的基本特點
(1)熱膨脹系數(shù)低(可調(diào)節(jié)):與Si、GaAs、AlN等無機(jī)陶瓷基片材料熱匹配良好;
(2)熱導(dǎo)率高:大大高于Kovar合金,可有效地擴(kuò)散大功率芯片產(chǎn)生的熱量;
(3)密度?。好芏却蟠蟮陀赪/Cu、Mo/Cu和Kovar合金,可有效減重;
(4)比強(qiáng)度和比模量高: 比模量是Kovar和W/Cu的4倍、Mo/Cu的2倍;
(5)AlSiC-鋁基碳化硅材料輕質(zhì)、熱膨脹系數(shù)可調(diào)匹配、熱導(dǎo)率高、價格適中。
按照不同的增強(qiáng)體,鋁基復(fù)合材料分為纖維增強(qiáng)和顆粒(直徑在0.5——100μm之間的等軸晶粒)增強(qiáng)、晶須增強(qiáng)鋁基復(fù)合材料。常用的增強(qiáng)顆粒主要包括SiC、Si3N4、Al2O3、TiC、TiB2、A1N、B4C以及石墨顆?;蛘呓饘兕w粒等。
常見的幾種鋁基復(fù)合材料的制備工藝有粉末冶金法、壓力浸滲工藝、反應(yīng)自生成法、高能高速固結(jié)工藝、半固態(tài)攪拌復(fù)合制造、噴射沉積法、攪拌摩擦加工法及球磨法制備納米碳管增強(qiáng)鋁基復(fù)合材料等。TiB2/A1復(fù)合材料的制備方法較多,主要有噴射沉積法、LSM、XDTM、擠壓鑄造、接觸反應(yīng)法、自蔓延高溫合成法和反應(yīng)機(jī)械合金化及粉末冶金法等。常見的方法有原位生成法、粉末冶金法、機(jī)械攪拌法、擠壓鑄造法、噴射沉積法、浸滲法等,下面主要對這六種方法進(jìn)行介紹。
原位生成法
原位生成法由Koczak 等人于 1989 年首次提出,其原理為按照材料預(yù)先設(shè)計的需求選取合適的反應(yīng)劑,然后在特定的環(huán)境下將溫度升到能使原料內(nèi)特定元素發(fā)生物理化學(xué)反應(yīng)的溫度,在這樣的條件下材料內(nèi)部能夠反應(yīng)生成一種或幾種均勻分布在基體內(nèi)部的且熱力學(xué)穩(wěn)定的增強(qiáng)體材料,以達(dá)到強(qiáng)化的效果。
原位內(nèi)生法的優(yōu)點在于原位生成的增強(qiáng)體顆粒在基體內(nèi)分布均勻,二者之間的界面干凈無污染、工藝簡單等,故而該方法具備廣闊的應(yīng)用前景,經(jīng)近幾十年的發(fā)展,已細(xì)化完善出了許多不同的制備工藝,比如:自蔓延高溫合成法、彌散放熱法、熔鹽輔助法和直接反應(yīng)法等。但是該方法也有一定的缺點,對于制備復(fù)合材料的原材料有一定要求,需要滿足一些反應(yīng)條件同時反應(yīng)的副產(chǎn)物的生成難以控制,另外還存在界面問題等。
粉末冶金法
粉末冶金工藝是最常采用的且最早用于制備納米顆粒增強(qiáng)鋁基復(fù)合材料的工藝之一。其制備過程是:先將陶瓷顆粒增強(qiáng)體與鋁合金基體粉末在球磨罐中均勻混合,混合過程既可以干混也可以在液體環(huán)境下進(jìn)行?;旌虾蟮姆垠w經(jīng)過冷壓成坯、真空排氣、熱壓燒結(jié)及后續(xù)處理(如擠壓、軋制、熱處理等)制得所需的復(fù)合材料。
粉末冶金工藝制備過程一般在真空或保護(hù)氣氛防護(hù)下進(jìn)行且燒結(jié)溫度低于鋁合金的熔點,從而大大的降低了發(fā)生界面反應(yīng)的可能性。粉末冶金法制備鋁基復(fù)合材料可以大范圍調(diào)控陶瓷顆粒的尺寸和含量,而且可以保證納米顆粒增強(qiáng)體在基體中較均勻的分布,減少團(tuán)聚與偏析的出現(xiàn),從而使復(fù)合材料得到增強(qiáng)。
該方法的缺點則在于材料容易出現(xiàn)氣孔,致密度不高。因此,必須通過擠壓、軋制或熱處理等工藝進(jìn)行二次處理以改善其致密度及機(jī)械性能。此外,粉末冶金制備工藝比較繁瑣,通常需要密封、真空或者保護(hù)氣氛的工作條件,而且燒結(jié)溫度選擇不當(dāng)會導(dǎo)致偏析。
機(jī)械攪拌法
機(jī)械攪拌法是在攪拌的過程中將增強(qiáng)體顆粒加入到基體金屬液中,利用高速旋轉(zhuǎn)的攪拌裝置使增強(qiáng)體均勻混合入基體金屬液之中,然后澆入模具中得到想要的鑄件。其生產(chǎn)設(shè)備見圖2所示。機(jī)械攪拌法操作過程較為簡單,成本低廉,不到其他加工工藝的一半,是可以廣泛應(yīng)用的方法,目前工業(yè)上制備復(fù)合材料大多數(shù)都是采用該方法。
綜合國內(nèi)外對攪拌鑄造的研究發(fā)現(xiàn),攪拌鑄造法可以以攪拌時的熔體溫度為依據(jù),將其分為液態(tài)攪拌和液半固態(tài)攪拌兩種方法。液態(tài)攪拌法主要是使攪拌溫度保持在液相線以上,一邊攪拌一邊加入增強(qiáng)體顆粒,攪拌之后可以直接進(jìn)行澆鑄。半固態(tài)攪拌是指將攪拌溫度調(diào)制固液相線之間,使熔體之中有一定的固相體積分?jǐn)?shù)。這樣在攪拌的時候熔體中會有更大的剪切力容易使增強(qiáng)體顆粒分布均勻。
這兩種方法各有優(yōu)缺點,液態(tài)法簡單,但是卷氣很嚴(yán)重,顆粒分散的不夠均勻。但是半固態(tài)攪拌鑄造法目前仍存在一些問題,如在攪拌過程中陶瓷顆粒容易產(chǎn)生偏聚、界面處易發(fā)生反應(yīng)等。其次,在空氣環(huán)境下進(jìn)行攪拌時,攪拌的過程中尤其是高速攪拌時很容易吸入氣體,使得最后澆鑄出的復(fù)合材料產(chǎn)品內(nèi)部出現(xiàn)有害的氣孔缺陷。再次,顆粒增強(qiáng)相添加的體積分?jǐn)?shù)有一定限制是利用攪拌鑄造法制備金屬基復(fù)合材料的另一個問題。
擠壓鑄造法
這種方法首先是要按照零件的形狀將增強(qiáng)體材料制備成預(yù)制塊,然后放入鑄型。在重力下澆注液態(tài)金屬或合金,隨后對金屬液施加壓力,使基體熔液滲入到預(yù)制塊中形成錠。
擠壓鑄造后得到的材料均勻性非常良好,材料內(nèi)部沒有明顯的缺陷。這是因為碳化硅顆粒與鋁合金基體的結(jié)合界面非常好,結(jié)合的十分緊密,使得二者之間的界面能夠起到傳遞載荷的作用,實現(xiàn)抑制鋁基體的膨脹的情況。
擠壓鑄造法還有諸多優(yōu)點:制備出的產(chǎn)品尺寸準(zhǔn)確穩(wěn)定,省去了后期二次加工的麻煩;金屬液浸滲的時間很短,因此能夠獲得很快的冷卻速度,這樣可以大大減少不良界面反應(yīng)的發(fā)生;加入增強(qiáng)相的量可以自由的調(diào)節(jié)其范圍。但是該方法工藝復(fù)雜,不利于用來成型形狀復(fù)雜的產(chǎn)品,而且如果使用浸滲的壓力比較大,可能會對產(chǎn)品形狀和模具的完好性產(chǎn)生很大的影響。
噴射沉積法
噴射沉積法是一種新型的加工工藝,主要是將熔化的基體金屬液在高速流動的惰性氣體中霧化向外噴出,同時將增強(qiáng)體顆粒添加到霧化噴出的金屬液體中,使兩者在沉降的過程中混合,最后共同在經(jīng)過預(yù)處理的基體上沉積制得想要的復(fù)合材料。
這種方法的優(yōu)點是可以隨意調(diào)節(jié)增強(qiáng)體相的體積分?jǐn)?shù),而且增強(qiáng)體材料的粒度大小在制備時也不受限制。得益于增強(qiáng)體顆粒與基體熔液之間接觸的時間很短暫,因此二者之間反應(yīng)時間非常有限,這樣可以明顯的改善二者之間的界面的結(jié)合狀態(tài)。因此霧化沉積技術(shù)可以使得基體保持快速凝固的特點,得到的晶粒十分細(xì)小。
浸滲法
浸滲法通常有兩種主要形式,包括無壓浸滲和壓力浸滲。無壓浸滲相對簡單,就是將基體Al合金在可控氣氛爐中加熱,使其超過液相線溫度;然后在不加壓力的條件下,使合金溶液自行浸滲到SiC預(yù)制體中去的制備方法。壓力浸滲的區(qū)別就是加上壓力條件,其方法接近于擠壓滲透鑄造。
浸滲法是一種成本較低且工藝簡單的制備技術(shù)。因而常用于高體積分?jǐn)?shù)SiCp/Al基復(fù)合材料的制備,制得的材料SiC顆分布相對均勻。成熟的無壓浸滲法制備的SiC/Al復(fù)合材料材料甚至已經(jīng)能夠應(yīng)用于電子封裝。但這種方法對預(yù)制體引入的高孔隙率難以控制。
以上就是本篇“AlSiC作為封裝材料的基本特點有哪些?”的全部內(nèi)容,想要了解更多,請持續(xù)關(guān)注本站。
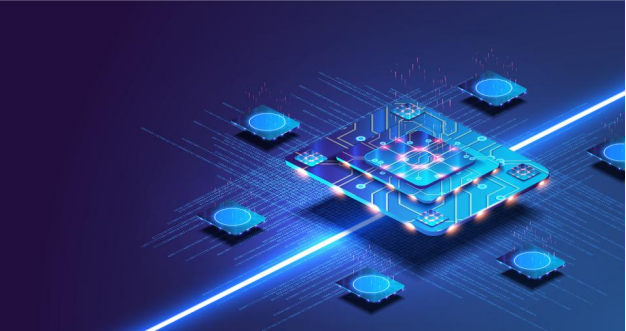
隨著物聯(lián)網(wǎng)、大數(shù)據(jù)和人工智能驅(qū)動的新計算時代的發(fā)展,對半導(dǎo)體器件的需求日益增長,同時也催生了市場對半導(dǎo)體材料的需求,半導(dǎo)體材料行業(yè)迎來快速發(fā)展的黃金期。在國家鼓勵半導(dǎo)體材料國產(chǎn)化的政策導(dǎo)向下,本土半導(dǎo)體材料廠商不斷提升半導(dǎo)體產(chǎn)品技術(shù)水平和研發(fā)能力,逐漸打破了國外半導(dǎo)體廠商的壟斷格局,推進(jìn)中國半導(dǎo)體材料國產(chǎn)化進(jìn)程,促進(jìn)中國半導(dǎo)體材料行業(yè)的發(fā)展。
數(shù)據(jù)顯示,2017-2019年中國半導(dǎo)體材料市場規(guī)模逐年增長,從2017年的76億美元增長至2020年的94億美元。據(jù)統(tǒng)計,2017-2020年全球62座新投產(chǎn)的晶圓廠中有26座來自中國大陸,占比超過40%,成為增速最快的地區(qū)。伴隨著5G時代的來臨,汽車電動化進(jìn)程拉動IGBT規(guī)模增長。得益于對清潔能源高速增長的需求,IGBT市場規(guī)模將持續(xù)增長,IGBT市場在2020年的規(guī)模為54億美元,從2020年到2026年將以7.5%的復(fù)合年增長率(CAGR)增長,預(yù)計2026年市場規(guī)模為84億美元。新能源車應(yīng)用作為IGBT市場規(guī)模的重要增量,2020年市場規(guī)模為為5.09億美元,2020-2026年的復(fù)合年增長率為23%,預(yù)計2026年新能源車用IGBT市場規(guī)模為17億美元。
隨著5G、智慧物聯(lián)網(wǎng)時代的到來,中國大陸的半導(dǎo)體產(chǎn)業(yè)得以在眾多領(lǐng)域?qū)崿F(xiàn)快速與全面布局,正逐步驅(qū)使全球半導(dǎo)體產(chǎn)業(yè)從韓國、中國臺灣向中國大陸轉(zhuǎn)移。目前,我國已經(jīng)成為最大的半導(dǎo)體市場,并且繼續(xù)保持最快的增速,預(yù)計半導(dǎo)體市場增長將持續(xù)帶動半導(dǎo)體材料行業(yè)快速發(fā)展。