淺識(shí)鋁碳化硅(AlSiC)
一、淺識(shí)鋁碳化硅(AlSiC)
鋁碳化硅(AlSiC)金屬基熱管理復(fù)合材料,是電子元器件專用電子封裝材料,主要是指將鋁與高體積分?jǐn)?shù)的碳化硅復(fù)合成為低密度、高導(dǎo)熱率和低膨脹系數(shù)的電子封裝材料,以解決電子電路的熱失效問題。
特性概況:1) AlSiC具有高導(dǎo)熱率(170~200W/mK)和可調(diào)的熱膨脹系數(shù)(6.5~9.5×10-6/K),因此一方面AlSiC的熱膨脹系數(shù)與半導(dǎo)體芯片和陶瓷基片實(shí)現(xiàn)良好的匹配,能夠防止疲勞失效的產(chǎn)生,甚至可以將功率芯片直接安裝到AlSiC基板上;另一方面AlSiC的熱導(dǎo)率是可伐合金的十倍,芯片產(chǎn)生的熱量可以及時(shí)散發(fā)。這樣,整個(gè)元器件的可靠性和穩(wěn)定性大大提高。
2) AlSiC是復(fù)合材料,其熱膨脹系數(shù)等性能可通過改變其組成而加以調(diào)整,因此電子產(chǎn)品可按用戶的具體要求而靈活地設(shè)計(jì),能夠真正地做到量體裁衣,這是傳統(tǒng)的金屬材料或陶瓷材料無法作到的。
3) AlSiC的密度與鋁相當(dāng),比銅和Kovar輕得多,還不到Cu/W的五分之一,特別適合于便攜式器件、航空航天和其他對(duì)重量敏感領(lǐng)域的應(yīng)用。
4) AlSiC的比剛度(剛度除以密度)是所有電子材料中最高的:是鋁的3倍,是W-Cu和Kovar的5倍,是銅的25倍,另外AlSiC的抗震性比陶瓷好,因此是惡劣環(huán)境(震動(dòng)較大,如航天、汽車等領(lǐng)域)下的首選材料。
5) AlSiC可以大批量加工,但加工的工藝取決于碳化硅的含量,可以用電火花、金剛石、激光等加工。
6) AlSiC可以鍍鎳、金、錫等,表面也可以進(jìn)行陽極氧化處理。
7) 金屬化的陶瓷基片可以釬焊到鍍好的AlSiC基板上,用粘結(jié)劑、樹脂可以將印制電路板芯與AlSiC粘合。
8) AlSiC本身具有較好的氣密性。但是,與金屬或陶瓷電子封裝后的氣密性取決于合適的鍍層和焊接。
9) AlSiC的物理性能及力學(xué)性能都是各向同性的。
由于AlSiC電子封裝材料及構(gòu)件具有高彈性模量、高熱導(dǎo)率、低密度的優(yōu)點(diǎn), 而且可通過 SiC體積分?jǐn)?shù)和粘接劑添加量等來調(diào)整膨脹系數(shù),實(shí)現(xiàn)與GaAs芯片和氧化鋁基板的熱匹配; 同時(shí)可近凈成形形狀復(fù)雜的構(gòu)件,因此生產(chǎn)成本也較低,使其在微波集成電路、功率模塊和微處器蓋板及散熱板等領(lǐng)域得到廣泛應(yīng)用。力學(xué)性能與用作結(jié)構(gòu)材料的鋁基復(fù)合材料相比, AlSiC 電子封裝材料的力學(xué)性能研究工作很少, 如果用作封裝外殼材料, 其力學(xué)性能也是結(jié)構(gòu)設(shè)計(jì)的重要數(shù)據(jù)。
SiC 體積分?jǐn)?shù)相同, 因基體合金和浸滲技術(shù)的不同, AlSiC 封裝材料的彎曲強(qiáng)度和彈性模量相差較大。
SiC體積分?jǐn)?shù)為70%時(shí), 與用 Al-Si-Mg系合金和無壓浸滲制備的復(fù)合材料相比, 用 AlSi20合金和擠壓鑄造技術(shù)制備的復(fù)合材料的彎曲強(qiáng)度提高了37%,但彈性模量降低 17%。SiC 體積分?jǐn)?shù)為60%和采用擠壓鑄造制備復(fù)合材料時(shí), 與基體為 AlSi12合金的相比, 基體合金為 Al-Cu4MgAg 的 AlSiC 封裝材料的彎曲強(qiáng)度和彈性模量分別提高73. 2% 和18%。
表1中所使用的基體合金,除 99. 7% Al 合金外, 其余均是可熱處理強(qiáng)化的合金, 改變熱處理工藝可獲取不同性能的封裝構(gòu)件, 如 60vol% SiCp/ AlCu4M gAg 封裝材料, 鑄造態(tài)和T6態(tài)的彎曲強(qiáng)度分別為 673. 2M Pa和 703. 5M Pa,而布氏硬度則分別為273和360。氣密性眾所周知, 氣密性是封裝材料及構(gòu)件的重要指標(biāo)之一, 氣密性不好會(huì)使外界水汽、 有害離子或氣體進(jìn)入封裝構(gòu)件中, 使封裝構(gòu)件產(chǎn)生表面漏電、結(jié)構(gòu)發(fā)生變化、 參數(shù)變化等失效模式。影響AlSiC 電子封裝材料氣密性的主要因素有: 制備工藝、 材料表面粗糙度等。如采用擠壓鑄造、 真空壓力浸滲和無壓浸滲制備AlSiC封裝材料, 材料孔隙率分別為 0. 7% ~ 3%、 0. 5% ~2%和 2. 9% ~ 5. 9%。為提高材料的氣密性, 必須減小材料中的孔隙率, 由于 AlSiC 中含有大量堅(jiān)硬的 SiC 粉末, 因此常采用熱等靜壓工藝進(jìn)行致密化處理。國外廠商生產(chǎn)的 AlSiC封裝材料的氣密性指標(biāo)都小于 10- 10 Pa?m3 / s。
分別采用真空壓力浸滲和無壓浸滲制備的 AlSiC 封裝材料的氣密性均能達(dá)到小于 5x 10- 9 Pa?m3 / s, 滿足了國軍標(biāo)對(duì)封裝材料氣密性的要求。
60%A1SiC復(fù)合材料25℃~100℃之間的平均線膨脹系數(shù)介于(6.7~8.4 ) x 10-6K-1之間, 低于常用封裝材料 Mo/10vol%Cu( 8.7x 10-6K-1)的熱膨脹系數(shù),能夠滿足電子封裝應(yīng)用的性能要求。
AlSiC 復(fù)合材料的熱膨脹系數(shù)隨著溫度升高而增加,在相同溫度下隨著SiC 顆粒體積分?jǐn)?shù)的增加而降低。對(duì)復(fù)合材料而言, 其熱膨脹系數(shù)主要取決于基體的熱膨脹系數(shù)和增強(qiáng)體通過基體 一增強(qiáng)體界面對(duì)基體的制約程度。一方面,由于鋁的熱膨脹系數(shù)隨溫度的提高而增大,導(dǎo)致復(fù)合材料的熱膨脹系數(shù)也隨溫度提高而增大。 另一方面,隨溫度提高,復(fù)合材料中增強(qiáng)體-基體界面?zhèn)鬏d能力下降,增強(qiáng)體對(duì)基體膨脹的制約能力降低,也導(dǎo)致復(fù)合材料熱膨脹系數(shù)隨溫度提高而增大。
導(dǎo)熱能力 表給出了不同體積分?jǐn)?shù)的AlSiC復(fù)合材料的熱導(dǎo)率測(cè)試結(jié)果,從中可以看出,50%AlSiC 復(fù)合材料室溫的熱導(dǎo)率在170W ( m?K )-1 左右,與傳統(tǒng)的高導(dǎo)熱封裝材W、Mo、Mo/10vol%Cu 的熱導(dǎo)率相近,是Kovar的10倍,已經(jīng)達(dá)到了電子封裝材料的高導(dǎo)熱要求。溫度對(duì)AlSiC復(fù)合材料的影響不大,但總體上呈現(xiàn)出隨溫度升高材料熱導(dǎo)率逐漸減小的趨勢(shì)。當(dāng)溫度相同時(shí),AlSiC復(fù)合材料的熱導(dǎo)率隨著體積系數(shù)的增大而減少。增強(qiáng)相體積分?jǐn)?shù)的增加,在復(fù)合材料內(nèi)部引入了大量的界面,這些界面的存在阻礙了熱傳導(dǎo)的進(jìn)行,使材料熱導(dǎo)率降低。
力學(xué)性能圖3是不同體積分?jǐn)?shù)下AlSiC復(fù)合材料的彎曲度。該材料的彎曲強(qiáng)度隨著SiC體積分?jǐn)?shù)的增加呈現(xiàn)減少趨勢(shì)。增強(qiáng)相體積分?jǐn)?shù)增加,復(fù)合材料的脆性增大,基體缺乏足夠的塑性來傳播很高的局部應(yīng)力,致使復(fù)合材料達(dá)到正常強(qiáng)度前斷裂。而且復(fù)合材料的強(qiáng)度還與增強(qiáng)相的大小、形狀以及材料的制備工藝有關(guān)。在顆粒含量、尺寸及內(nèi)部缺陷作用下,使得高體積分?jǐn)?shù)AlSiC復(fù)合材料的彎曲強(qiáng)度并不隨SiC體積分?jǐn)?shù)增大而增大。 圖4為AlSiC復(fù)合材料彎曲試樣斷口的掃描電子顯微鏡照片。從圖4中可以看到。對(duì)于體積分?jǐn)?shù)較高的復(fù)合材料整體上呈現(xiàn)出脆性斷裂的特征,但在復(fù)合材料斷口中存在少量的撕裂棱和韌窩,具有一定的塑性變形的特征。體積相分?jǐn)?shù)越高,材料脆性斷裂的特征就越明顯。
以上本篇“淺識(shí)鋁碳化硅(AlSiC)?”的全部內(nèi)容,想要了解更多,請(qǐng)持續(xù)關(guān)注本站。
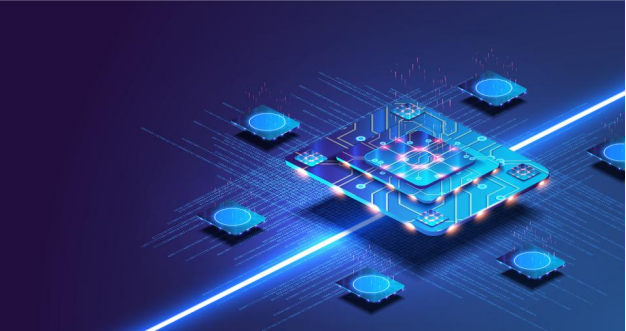
隨著物聯(lián)網(wǎng)、大數(shù)據(jù)和人工智能驅(qū)動(dòng)的新計(jì)算時(shí)代的發(fā)展,對(duì)半導(dǎo)體器件的需求日益增長,同時(shí)也催生了市場對(duì)半導(dǎo)體材料的需求,半導(dǎo)體材料行業(yè)迎來快速發(fā)展的黃金期。在國家鼓勵(lì)半導(dǎo)體材料國產(chǎn)化的政策導(dǎo)向下,本土半導(dǎo)體材料廠商不斷提升半導(dǎo)體產(chǎn)品技術(shù)水平和研發(fā)能力,逐漸打破了國外半導(dǎo)體廠商的壟斷格局,推進(jìn)中國半導(dǎo)體材料國產(chǎn)化進(jìn)程,促進(jìn)中國半導(dǎo)體材料行業(yè)的發(fā)展。
數(shù)據(jù)顯示,2017-2019年中國半導(dǎo)體材料市場規(guī)模逐年增長,從2017年的76億美元增長至2020年的94億美元。據(jù)統(tǒng)計(jì),2017-2020年全球62座新投產(chǎn)的晶圓廠中有26座來自中國大陸,占比超過40%,成為增速最快的地區(qū)。伴隨著5G時(shí)代的來臨,汽車電動(dòng)化進(jìn)程拉動(dòng)IGBT規(guī)模增長。得益于對(duì)清潔能源高速增長的需求,IGBT市場規(guī)模將持續(xù)增長,IGBT市場在2020年的規(guī)模為54億美元,從2020年到2026年將以7.5%的復(fù)合年增長率(CAGR)增長,預(yù)計(jì)2026年市場規(guī)模為84億美元。新能源車應(yīng)用作為IGBT市場規(guī)模的重要增量,2020年市場規(guī)模為為5.09億美元,2020-2026年的復(fù)合年增長率為23%,預(yù)計(jì)2026年新能源車用IGBT市場規(guī)模為17億美元。
隨著5G、智慧物聯(lián)網(wǎng)時(shí)代的到來,中國大陸的半導(dǎo)體產(chǎn)業(yè)得以在眾多領(lǐng)域?qū)崿F(xiàn)快速與全面布局,正逐步驅(qū)使全球半導(dǎo)體產(chǎn)業(yè)從韓國、中國臺(tái)灣向中國大陸轉(zhuǎn)移。目前,我國已經(jīng)成為最大的半導(dǎo)體市場,并且繼續(xù)保持最快的增速,預(yù)計(jì)半導(dǎo)體市場增長將持續(xù)帶動(dòng)半導(dǎo)體材料行業(yè)快速發(fā)展。